Brief overview of aluminum castings and their common issues
Looking for a reliable solution to enhance your welding tasks? We understand the importance of finding the right equipment that meets your needs, and that’s why we’re here to introduce you to our top-of-the-line welders. Whether you’re a beginner or a seasoned professional, our welders are built to withstand the most demanding challenges, including welding aluminum castings.
Aluminum castings have become increasingly popular in various industries due to their lightweight properties and exceptional strength. From automotive parts to aerospace components, aluminum castings offer numerous benefits. However, working with aluminum castings can present some common issues, as with other welding projects. However, the right tools and techniques can easily overcome these challenges.
One common issue you may encounter when welding aluminum castings is the formation of porosity. Porosity refers to small holes or voids that can develop during welding, creating weak spots in the structure. This issue often arises due to aluminum’s high thermal conductivity, which makes it challenging to avoid trapping gases during the solidification process. However, fear not; our reliable welders have advanced features that effectively minimize porosity, ensuring a strong and sturdy welding joint.
Another potential challenge you may face is the presence of oxide layers on the surface of aluminum castings. Aluminum readily reacts with oxygen in the air, forming a thin layer of oxide that can hinder proper bonding during welding. Our welders offer superior arc control and precise heat input, allowing you to remove these oxide layers efficiently, resulting in a clean and flawless weld.
Moreover, achieving proper penetration when welding aluminum castings can sometimes be tricky. Aluminum’s heat conductivity can cause rapid heat dissipation, leading to insufficient heat penetration and a weak weld joint. Our welders boast exceptional power and control, ensuring you consistently achieve the desired weld penetration.
In conclusion, welding aluminum castings can be rewarding, yielding high-quality, lightweight structures. However, having the right equipment to handle the specific challenges associated with aluminum welding is crucial. Our welders are designed to meet the needs of people like you, offering state-of-the-art features that effectively address the common issues faced in aluminum casting welding. Trust our welders to simplify your welding journey, providing you with the strength and precision required for successful aluminum casts. Don’t hesitate any longer – invest in our top-notch welders to take your welding projects to new heights!
Importance of proper repair techniques for aluminum castings
Hey there, fellow welding enthusiasts! We’re here to discuss the importance of proper repair techniques for aluminum castings. Whether you’re a seasoned pro or just getting started in welding, this is a crucial aspect you can’t afford to overlook. Your welding skills are only as good as the techniques you employ, and when it comes to repairing aluminum castings, doing it right is essential.
Aluminum castings are widely used in numerous industries, from automotive to aerospace. They offer lightweight and versatile properties, making them popular for many applications. However, due to their unique characteristics, repairing damaged aluminum castings requires special attention. And that’s where your welding skills and the right equipment come into play.
One of the most important factors to consider when repairing aluminum castings is heat management. Aluminum has a low melting point, which makes it more susceptible to distortion and warping if not handled adequately during welding. That’s why having a welder designed explicitly for aluminum repair is paramount.
Utilizing a high-quality welder designed for aluminum castings ensures that the heat input is controlled and consistent. This will minimize the risk of overheating and prevent any potential damage to the castings. Welding professionals know that controlling heat is key to achieving quality welds, and this holds when it comes to repairing aluminum castings.
Moreover, using the proper techniques and equipment will ensure that your welds are strong and aesthetically pleasing. Aluminum castings are often visible in finished products, and having clean, smooth welds adds to their overall appeal and functionality. It’s all about delivering a high-quality repair that will stand the test of time.
At [Welder Manufacturer], we understand the importance of proper repair techniques for aluminum castings. That’s why our range of welders is specifically designed to cater to the unique challenges of welding aluminum. We’ve incorporated cutting-edge technology and intelligent features that make repairing aluminum castings a breeze for both novice and experienced welders.
So, whether you’re working on automotive parts, aircraft components, or any other aluminum casting repair job, investing in the right welder is worth every penny. Don’t settle for subpar results when superior quality repair is within reach. Choose a welder tailored for aluminum castings and unlock your full welding potential.
Remember, proper repair techniques for aluminum castings go a long way in ensuring the longevity and durability of your welds. Equip yourself with the right tools, hone your skills, and let your welding expertise shine. So, what are you waiting for? It’s time to get a top-notch welder and take your aluminum casting repairs to the next level!
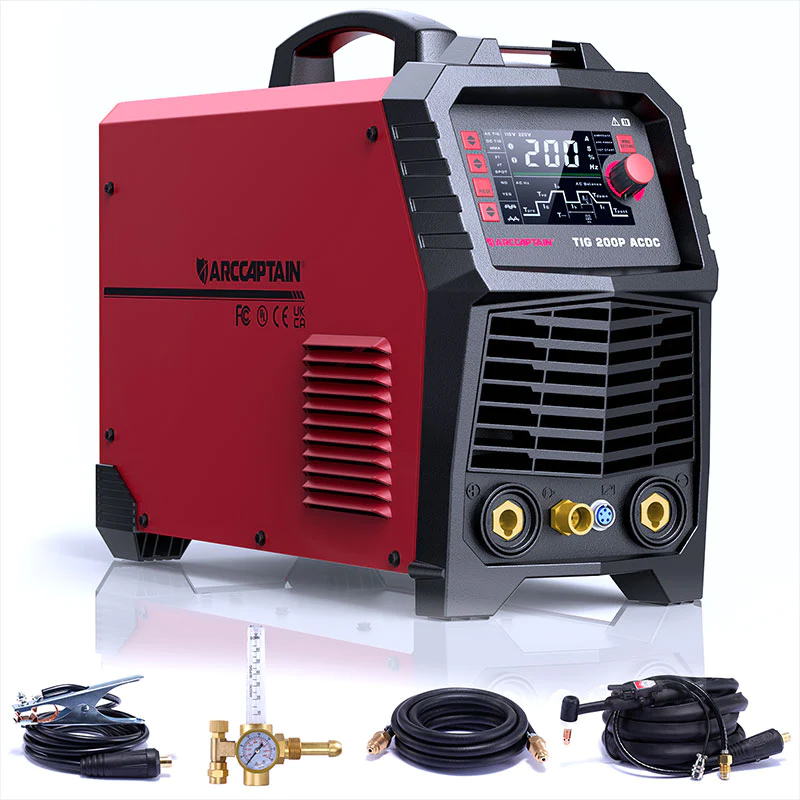
Understanding Aluminum Castings
Are you an experienced welder looking to expand your skill set? Or perhaps you’re a novice welder eager to take on new challenges? No matter your level of expertise, understanding aluminum castings can open up a whole new world of possibilities.
Aluminum is a highly versatile material widely used in various industries, such as automotive, aerospace, and construction. Its lightweight yet strong properties make it an ideal choice for many applications. However, welding aluminum can be pretty different from welding other metals, so having the right equipment is crucial.
Investing in a high-quality welder designed explicitly for aluminum castings allows you to take on projects involving repairing or fabricating aluminum components efficiently. These welders are engineered to handle aluminum’s unique characteristics, enabling you to always achieve clean and precise welds.
One key factor to consider when working with aluminum castings is the heat input. Unlike other metals, aluminum has a higher thermal conductivity, which dissipates heat more rapidly. This can pose a challenge, as excessive heat can adversely affect the weld and cause distortion or structural issues. Fortunately, modern welders have innovative features such as adjustable heat settings and pulse welding capabilities that allow you to control the heat input effectively.
Another essential aspect to understand about aluminum castings is using appropriate filler materials. Aluminum alloys come in various grades, requiring specific filler materials to ensure a strong and reliable weld. Using a welder designed for aluminum gives you access to a range of compatible filler materials, ensuring that your welds are of the highest quality.
Furthermore, welding aluminum castings requires cleanliness and proper preparation. Aluminum oxidizes quickly, forming a thin layer of oxide that hinders proper bonding. To overcome this, specialized welders often incorporate pre-weld cleaning functions that remove the oxide layer, ensuring optimal weld quality and strength.
Investing in a welder specifically tailored for aluminum castings expands your capabilities as a welder and provides a safe and efficient welding experience. These welders are designed with user-friendly interfaces, advanced safety features, and durable construction, all essential for the demanding requirements of welding aluminum.
So, if you’re ready to take your welding skills to the next level and embrace the world of aluminum castings, investing in a high-quality welder is a smart decision. With the right equipment, you’ll be able to tackle any aluminum welding project with confidence, delivering exceptional results that will impress people across various industries. Don’t miss out on the opportunities that welding aluminum castings can bring—get your professional welder today!
Definition and characteristics of aluminum castings
Are you a skilled welder looking to expand your capabilities and take on a new range of projects? One material that you should consider working with is aluminum. Aluminum castings have gained immense popularity in various industries due to their unique properties and versatility. In this article, we will delve into the definition and characteristics of aluminum castings, shedding light on why investing in a welder designed for working with aluminum can greatly benefit your work.
To put it simply, aluminum castings are metal structures created by pouring liquid aluminum into a mold and allowing it to solidify this process. This process is known as casting, which results in custom-made components that are both lightweight and incredibly strong. The popularity of aluminum castings can be attributed to their outstanding corrosion resistance, high thermal and electrical conductivity, and impeccable dimensional stability. These characteristics make aluminum castings an ideal choice for aerospace, automotive, and construction industries.
One key advantage of working with aluminum castings is their unrivaled strength-to-weight ratio. Aluminum is significantly lighter than other metals, such as steel, allowing you to create sturdy and durable parts without adding unnecessary weight. This lightweight nature not only improves the overall efficiency of your project but also reduces fuel consumption, making it an economical choice in the long run.
Moreover, aluminum castings boast exceptional heat transfer properties. This means they can quickly dissipate heat and efficiently cool down, making them perfect for applications where temperature regulation is crucial. Whether you’re tasked with fabricating heat exchangers or cooling systems, aluminum castings will ensure optimum performance and longevity.
Another noteworthy characteristic of aluminum castings is their exceptional corrosion resistance. Unlike other metals, aluminum naturally forms a thin protective oxide layer upon exposure to air, preventing further rust or oxidation. This inherent corrosion resistance ensures that your components are durable and require minimal maintenance, saving you precious time and money.
Regarding precision and dimensional stability, aluminum castings once again prove their worth. The casting process allows for intricate designs and complex geometries to be achieved, ensuring that your creations are ideally suited for your intended use. Additionally, aluminum castings demonstrate impeccable dimensional stability, meaning they retain shape and size even under extreme stress or fluctuating temperatures.
To fully harness the benefits of aluminum castings, it is crucial to invest in a welder engineered explicitly for working with aluminum. These welders are designed to handle aluminum’s unique characteristics, ensuring clean, precise, and efficient welds. From TIG welders to MIG welders, various options are available that cater specifically to aluminum welding, making it easier for you to achieve impeccable results.
In conclusion, investing in a welder designed for working with aluminum is a smart move for any skilled welder looking to expand their capabilities and cater to a broader range of projects. With the exceptional properties of aluminum castings, you can create lightweight, corrosion-resistant, and dimensionally stable components that will excel in various applications. So why wait? Upgrade your welder and embrace the world of aluminum castings today!
Common issues with aluminum castings that may require repair
Hey there, passionate welders and DIY enthusiasts! If you’re reading this, chances are you love working with metal and understand the unparalleled satisfaction that comes from crafting something with your own two hands. Whether you’re a seasoned professional or just starting your welding journey, having the right tools is essential.
Now, let’s talk about a common challenge many face when working with aluminum castings – repair. While aluminum castings offer numerous benefits, such as lightweight properties and excellent heat conduction, they are not immune to issues. But fear not, for a simple and effective solution is waiting for you – your very own welder.
One of the most common problems encountered with aluminum castings is porosity. This occurs when tiny air pockets are trapped within the material, leading to weakened structural integrity. Whether dealing with porosity in engine blocks or intricate parts, such imperfections can compromise castings’ overall performance and durability.
Then there’s the issue of worn-out or damaged components. Over time, due to constant usage or exposure to harsh environments, aluminum castings can experience wear and tear. When left unaddressed, this can adversely affect the functionality and reliability of the finished product.
But don’t be disheartened! With the right welding equipment, you can effortlessly tackle these common problems. A welder specifically designed for aluminum applications empowers you to repair porosity and restore the casting’s strength. By skillfully welding the affected areas, you ensure the finished part is built to withstand time.
Additionally, when components are worn or damaged, you can count on your welder to rescue you. By skillfully joining new aluminum pieces or repairing existing ones, you can restore the casting to its former glory. There is no need to spend excessive time or resources on sourcing replacements when you have the power to fix it yourself.
Investing in a high-quality welder allows you to repair aluminum castings when problems arise and offers you the creative freedom to explore new horizons in metalworking. With your welder, you can effortlessly experiment with different designs, create custom pieces, and take your projects to the next level.
Remember, people who are serious about their craft invest in reliable tools. So, if you’re ready to overcome the common issues that come with aluminum castings and unlock a world of possibilities, it’s time to consider adding a welder to your arsenal. Embrace the joy of being in command of your creations and say goodbye to the limitations of pre-made parts. Trust us; you won’t regret it!
Welding Aluminum Castings
Hey there, fellow welding enthusiast!
Have you ever tried welding aluminum castings? If you have, you know how challenging it can be to achieve a sturdy and durable weld. But fear not! We have the perfect solution for you—a high-quality welder specifically designed for this purpose.
Aluminum castings are widely used in various industries due to their lightweight and excellent heat conductivity properties. The demand for welding aluminum castings is increasing rapidly from automotive parts to aerospace components. So, investing in the right welder is a must if you want to stay ahead of the game and broaden your welding capabilities.
Why is it important to choose the right welder for aluminum castings? Well, welding aluminum castings requires a delicate balance of heat and precision. Unlike welding steel, aluminum has a higher heat conductivity, meaning heat dissipates quickly. Therefore, you need a welder that can provide consistent and controlled heat input to achieve a smooth and strong weld.
Our welders are engineered with cutting-edge technology to meet the requirements of welding aluminum castings. With advanced heat control systems, you can precisely adjust the heat input to prevent overheating or underheating the casting, ensuring optimal weld quality. This means you can confidently weld complex aluminum castings without compromising their structural integrity.
But that’s not all! Our welders also offer increased productivity and efficiency. With features like high welding speeds and user-friendly interfaces, you can complete your welding projects in a fraction of the time. This means more time for you to take on new projects and ultimately increase your bottom line.
Moreover, our welders are built to last. We understand that people like you depend on their equipment day in and day out. We’ve crafted our welders with high-quality materials and robust construction. So, whether you’re working in a demanding industrial setting or a home workshop, our welders will stand the test of time and deliver consistent performance for years to come.
So, don’t let the challenges of welding aluminum castings hold you back. Equip yourself with the right welder and unlock a new world of possibilities. Whether you’re a professional welder or a passionate DIYer, our reliable and efficient welders will help you achieve exceptional results.
Ready to improve your welding skills? Explore our range of welders today and join the growing community of skilled welders who trust our products. Happy welding!
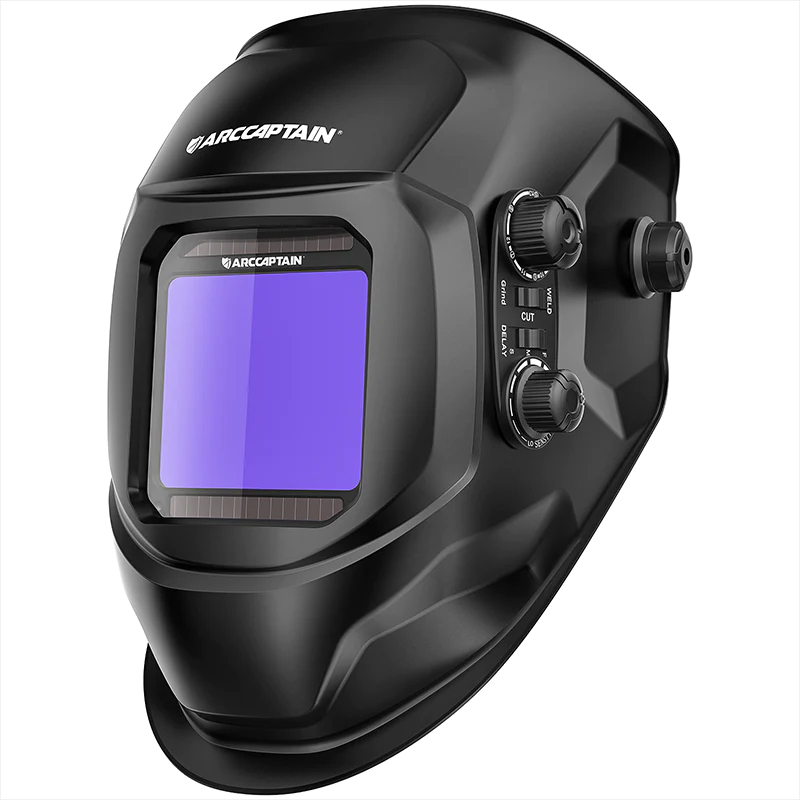
Overview of the welding process for aluminum castings
Looking to enhance your welding capabilities? Are you ready to step up your game and take on aluminum castings? Look no further! Our top-of-the-line welders, including aluminum castings, are the perfect fit for your welding needs. With our cutting-edge technology and superior craftsmanship, we guarantee that our welders will exceed your expectations.
But before we delve into the benefits of our welders, let’s talk about the welding process for aluminum castings. Whether working on automotive parts, marine structures, or aerospace components, welding aluminum castings requires precision and finesse. Aluminum, known for its lightweight yet sturdy properties, poses unique challenges during welding.
One of the first things to consider when welding aluminum castings is the choice of equipment. Our welders offer advanced features specifically designed to handle aluminum welds with ease. The precise control settings allow you to achieve optimal heat, ensuring a strong and durable weld joint.
Next, let’s discuss the welding technique. A popular method for working with aluminum castings is Tungsten Inert Gas (TIG) welding. TIG welding minimizes the risk of impurities, producing clean and aesthetically pleasing welds. Additionally, TIG welding grants excellent control over the heat input, preventing distortion and ensuring structural integrity.
To achieve high-quality welds on aluminum castings, preparing your workspace appropriately is imperative. Proper cleaning and degreasing of the castings remove any contaminants that might hinder the welding process. Our welders’ user-friendly interface allows you to adjust the settings and enable precise control over the arc, ensuring superior weld appearance and minimizing defects.
Additionally, remember to choose the right filler material. Aluminum-copper alloys are commonly used for welding cast aluminum due to their compatibility and strength. Our welders provide exceptional arc stability, making it easier to control the filler material and ensuring consistent penetration.
Lastly, safety should always be a priority. Proper ventilation and protective gear are crucial when welding aluminum castings. Our welders have safety features that prioritize your well-being and provide peace of mind.
In conclusion, investing in our top-notch welders is a no-brainer if you’re serious about welding aluminum castings. With features tailored to tackle the challenges of aluminum welding, our welders give you the edge you need. So, join the countless people who have revolutionized their welding game – choose our welders and see the remarkable difference they make in your aluminum casting projects!
Challenges with welding aluminum
Title: Mastering Aluminum Welding: Overcoming Challenges with Top-Quality Welders
Introduction:
Welcome, fellow welders! Are you ready to conquer the world of aluminum welding? We know that mastering this particular skill is not without its challenges. However, armed with the right knowledge, techniques, and equipment, you can effortlessly conquer every obstacle that comes your way. Today, we’ll discuss some common challenges faced during aluminum welding and how investing in a top-quality welder can make all the difference. Let’s dive in!
1. Heat Management:
Aluminum has high thermal conductivity, meaning it rapidly dissipates heat. One of the biggest challenges welders face is efficiently managing this heat during welding. Without proper heat control, you risk burning through the thin aluminum sheets or creating weak and brittle welds. That’s where a reliable welder comes in!
Our state-of-the-art welders are equipped with advanced heat management systems. With precise temperature control and adjustable pulse settings, you can fine-tune the heat input to match the specific requirements of your aluminum welding projects. Say goodbye to warped materials and say hello to clean and smooth welds!
2. Oxidation and Contaminants:
Aluminum readily reacts with oxygen in the air, forming an oxide layer on its surface. This oxide layer acts as a barrier, hindering the fusion process and compromising the integrity of your welds. Contaminants such as grease, dirt, or even moisture can further exacerbate the issue. However, fret not! A top-quality welder can help you combat these challenges with ease.
Our advanced welders employ innovative features like pulsed TIG technology, which reduces the heat-affected zone, limiting oxidation and improving the welding process. Precise shielding gas controls ensure a protective environment, preventing contamination and superior weld quality. You’ll achieve reliable and visually appealing welds every time!
3. Aluminum Alloy Compatibility:
Aluminum alloys come in various grades, requiring specific welding techniques and considerations. Understanding the alloy, you’re working with is essential for achieving optimal results. However, fear not, as our welders offer versatility to accommodate different aluminum alloys and thicknesses.
Whether you’re handling 6000 series or 5000 series aluminum, our welders provide the flexibility to adjust critical parameters, such as arc balance, AC/DC power, and pulse frequency. With the ability to fine-tune these settings, you’ll effortlessly tackle any aluminum alloy, ensuring strong and defect-free welds.
Conclusion:
Welding aluminum doesn’t have to be a daunting task. Embracing the challenges head-on and equipping yourself with a top-quality welder can empower you to master this skill like a pro. Our welders offer the tools you need to overcome the hurdles of heat management, oxidation, and compatibility with various aluminum alloys. With their advanced features and reliable performance, your aluminum welding projects will never be the same again.
Leap and choose a welder that understands the unique demands of aluminum welding. Invest in a welder who makes your work easier, eliminates frustrations, and brings out the best in your craftsmanship. With our top-quality welders by your side, you’ll be well on your way to achieving remarkable results in all your aluminum welding endeavors. Let’s create, let’s shape, let’s Weld with Confidence!